METHOD STATEMENT FOR CONCRETE WORK
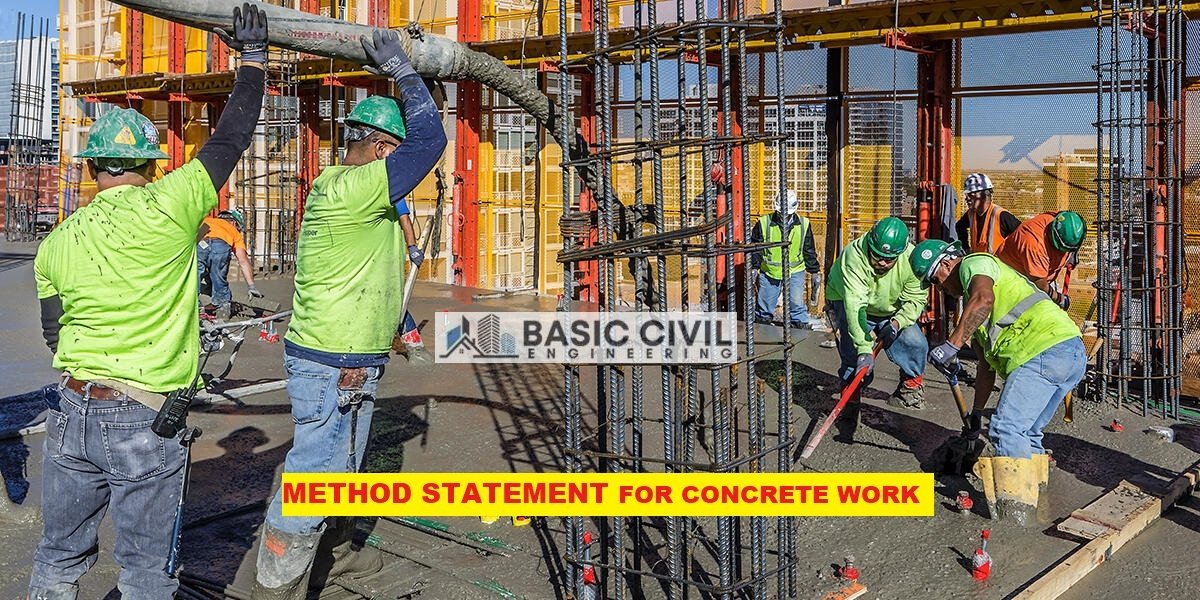
Method Statement for Concrete Work
1. Purpose:-
- This method is developed to discuss the procedural work to be carried out during the performance of Civil Works – Foundation and Concrete Works in the context of D&C of Professional Accommodation Village – site F-5040 Units Project. The works involve the fabrication and installation of formworks, Installation of reinforcing bars and concrete pouring.
- Inspection and testing during the implementation of all the foundation and concrete works will be carried out according to the issued Inspection and Test Plans with respect to the type and frequency of the testing.
- Hazard analysis will be conducted prior to the start of site activities to identify and assess any Health, Safety and Environmental Issues which may have an impact on the construction of these structures.
- The purpose of this Method Statement therefore, is to outline the safe system of work which will be adopted during the course of construction.
2. Scope of Work:-
This Method Statement covers the detailed description and sequence of work execution that is enhanced further with technical sketches to support and to express concisely the following elements to be constructed including formworks, supports, embeds and accessories. This method statement is applicable for all concreting work.
3. Methodolog:-
3.1 Sequence of Activities:-
As a brief review of all the structure activities and based on the drawings and technical documents available, our best interpretation is being illustrated in the following sections.
3.1.1 Formworks and Reinforcing Bars:-
- Formworks shall be pre-fabricated at workshop by panels. Panels shall be based on the required dimension as per IFC drawings.
- The Panel composition is basically consisting of laminated marine plywood and reinforced with timber framing to increase its strength. The plywood shall be fastened together with the timber frame using a 2 in. nail to every 18mm thick. Plywood. The plywood is dimensioned to form a medium size panel so it comes to be lighter and easy to handle during installation.
- Epoxy Coated reinforcing bars shall be ordered only on the approved supplier of Company / Contractor. As much as possible all reinforcing bars shall be ordered pre-fabricated based on approved bar bending schedule. In some cases, where it is necessary, fabrication shall be done at site or at company workshop using electric cutter and electric rebar bending machines. All cut & bend coated bars, cut ends & bends coating damages to be painted with approved touch up paint.
- All lengths and sizes of rebar’s shall be based on the approved bar cutting/bending schedule. FBE coated reinforcing bars shall be properly stored , not touching the ground directly and covered to avoid contamination from windblown dust. Prior to pouring, rebar shall be clean and dust free.
3.1.1.1 Footing Formworks and Re-bar:-
The work procedure of foundation formwork is divided in to 3 parts.
- Preparation & Fabrication of Panel.
Generally, preparation of panel takes place before setting out or while excavation work is being Formwork carpenter will prepare panel in the carpentry workshop area.
- Layout of footing.
Using surveying instrument such as Total Station, dimension of the foundation based on IFC drawings shall be transferred to the previously poured lean concrete.
- Assembly of Footing Foundation Formwork.
Position the formwork over the Brace the panel and secure it by nailing braces to lean concrete surfaces. See figure 3 & 3A.
FIGURE 3
FIGURE 3A
- After bracing the four faces as shown in 4, the formwork is ready for Reinforcement work.
FIGURE 4
Note: Check the drawings and panel schedule to select the correct panels
- Transport the panels required to the work area.
- Joint the four pieces’ panels using 2-1/2” nails.
3.1.1.2 Lay in of Preassembled Footing Bars:-
In order to secure the stub or starter bar at the correct position, a piece or 2 pieces of timber are nailed to the side panel and stub/starter main bar tied to it. Both formwork and reinforcement Worker can perform the work.
FIGURE 5
Key point
- Bracing should be strong enough to prevent buckling or swaying.
- Timber ties/lateral supports across the panel are to be used, especially if the size of Footing is large.
- Panel should be levelled, plumb, square, straight and smooth.
3.1.1.2 Installation of PVC Spacer:-
Install Concrete spacer having similar compressive strength of structural concrete to maintain required concrete cover.
3.1.12 Submission of Work Request Inspection (WIR):-
Submit Work Inspection Request for casting of concrete footing Refer to Contractor QCP forms and relevant request slips.
When everything is cleared, proceed to concreting procedure.
Form stripping shall be as per guidelines indicated in ACI 347- 01 clause 3.7, entitled
“Removal of Forms and Support” (Figure 6)
Item No. |
Type of Formwork |
Minimum Period | Before Removal |
16 Deg. C | 7 Deg. C | ||
1 |
Vertical Formwork to Columns , Walls and Large Beams |
12 Hrs. |
18 Hrs. |
2 |
Joist Beam or Girder Soffit with less than 3M span and between structural supports |
4 days |
7 days |
3 |
Joist Beam or Girder Soffit with 3M to 6M clear span and betwee structural supports. |
7 days |
14 days |
4 |
Joist Beam or Girder Soffit with more than 6M span and betwee structural supports |
14 days |
21 days |
5 | Center of an Arch | 7 days | 14 days |
6 |
One way floor slabs with less than 3M clear span betwee structural supports |
3 days |
4 days |
7 | One way floor slabs with 3M to 6M clear span between structura supports | 4 days | 7 days |
8 |
One way floor slabs with more than 3M clear span betwee structural supports |
7 days |
10 days |
3.1.2 Pillars / Columns:-
Following the required curing time for footing and form removals, activities to the column may proceed after at least 12 hours.
- Erect the steel bars and splice to the starter bars as per IFC drawing Should it be required to install supports of the bar to prevent from sway and depletion, a temporary wooden brace or may be an appropriate guy wire should be installed to pillar / column bars.
Note:
Column bar to be spliced shall depend to the type of structure to be constructed. Shorten Bars for a foundation only and long bar for an elevated structure as illustrated on the following figure.
- Before installation of forms, make sure that the surface of the hardened concrete that will come in contact with the new concrete is thoroughly scraped and cleaned in a manner that shall not leave loosened particles of aggregate or damaged concrete and shall be thoroughly cleaned of foreign matter and laitance.
- Install the four sides of the pillar forms with surfaces applied with approved type of form release agent.
- Check the alignment of end pillar by using Total station surveying equipment.
- Clamp or fasten the four sides tightly to ensure that all surfaces are snag fit not to allow Concrete slurry to drip thru joints.
- Provide side supports as required to ensure alignment.
- Install all necessary embedded materials (if required) such as anchor bolts or insert plates as per IFC drawings. Installation of inserts shall be based on Technip-Issued Standard Construction Drawings for Concrete Works.
- Upon completion, request for Work Inspection Request (WIR).
- Proceed with concrete pouring as prescribed in 2 Concrete Works.
- Strip off forms as per guidelines in Table of 6 above..
- Proceed to curing as prescribe in the following section.
3.1.3 Concreting Work:-
- Concrete as supplied by Approved ready mix supplier shall be used.
- The surface to receive concrete shall be clean maybe wetted, but standing water shall be removed prior to concrete pouring.
- The placement of concrete shall commence only after all approvals have been obtained.
- Pump car equipped with hose of adequate length shall be used.
3.1.3.1 Material:-
Approved Ready mix supplier shall supply the concrete as per material submittal Proposed by Company and approved and in compliance with the requirement of the Project Specifications.
3.1.3.2 Slump Test, Temperature and Concrete Cylinder Specimen:-
- Slump test and temperature control shall be performed for every truck arriving on site prior to dump concrete. Any delivery that fails to meet the slump test requirements or has a temperature exceeding 32°C shall be rejected.
- Test cylinders shall be made from concrete for every 50m³ & shall keep cylinders under the sheds. The cylinder specimen shall be tested for compressive strength in accordance with the Client / Contractor’s Standard, Approved Ready Mix Concrete, and in conformance with the approved project Quality Control Procedures.
- Collecting a Minimum SiCylinderser for every 50m³ for the Compressive Strength
- Compressive Strength Report for 7 & 28.
3.1.3.3 Procedure:-
- After getting all required inspections, the pouring is to be started.
- Re-check for all the arrangements and manpower/eqequipment equired.
- The concrete sequence of placing of concrete shall progress from the bottom at every about 300-400mm per layer throughout the foundation.
- Concrete shall not be dropped freely where reinforcing bar may be segregated and not freely dropped from more than 1m. Concrete shall be deposited as near as possible in its final position, to avoid segregation due to handling.
- Every layer shall be carefully compacted by using concrete vibrators.
- One concrete pump and sufficient number of concrete delivery transit mixer trucks are to be deployed for every pouring of the foundation.
- Pump mix concrete slump to be checked for placing of concrete when using concrete pump.
- Plastic sheeting or canvas sheeting’s are to be laid to cover the concrete surface to protect and in case of rain during concreting operation.
- Lighting facilities are to be provided during the night pouring of concrete.
- If the air temperature is less than 30°C concrete shall be placed within 90 minutes of the introduction of the mixing water to the cement and aggregate or cement to aggregate. If the air temperature is greater than 30°C mixing time shall be reduced and concrete placed within 60 minutes except when a suitable set retarding mixture is used and slump requirements can be met. The maximum time between batching and placing shall not exceed 120 minutes in all cases.
- The minimum concrete cover detailed in the project specification shall be met.
- for 50 cum 8 cylinder shall be taken.
- As per ACI 305.1-06 before hot weather concreting and the pre-installation conference, the Contractor shall submit to Engineer for review and approval a detailed plan and procedures proposed to reduce or avoid the potential problems of hot weather concreting, including production, placement, finishing, curing, and protection of concrete during hot weather concreting.
- Developing a comprehensive plan and procedures for use in hot weather concreting conditions include the following practices and measures used to reduce or avoid the potential problems of hot weather concreting.
- Select concrete materials and proportions with satisfactory records in hot weather conditions that have been by testing to be satisfactory.
- reducing and controlling the temperature of fresh
- Sing a concrete mixture with sufficient workability that will permit rapid placement and effective consolidation.
- Minimizing the time to transport, place, consolidate, and finish the concrete.
- Scheduling of placing operations during times of the day or night when
WaterStops.
A- Flexible rubber waterstop, complying with CDR-C-513 code, for embedding in concrete to prevent passage of fluids through joints. Manufactured by such a process that they will be dons, homogenous, and free from holes and other imperfections.
B- Flexible PVC waterstops, complying with CDR-C-572 code, will be used in Couns- Ruction joints, for underground structures, or were show on contract drawings Manufactured by such a process that they will be dons, homogenous, and free from holes and other imperfections.
3.1.3.4 Curing:-
All water to be used shall comply with the requirements for mixing water. Concrete curing by using water when the concrete is hardened, the concrete surface shall be covered with burlap, etc. and sprinkled with potable water to keep the concrete surface wet. Concrete curing shall continue for minimum 7 days & Curing compound for the vertical structures such as walls and columns. The saturated burlaps shall be covered with a plasticized sheet vapor barrier, minimum 0.15mm in thickness.
3.1.3.5 Concrete Protection and Grouting Work:-
Underground concrete protection such as coal tar epoxy coating and polyethylene sheet laying method statement shall be submitted separately. Grouting works shall also be submitted separately.
- Provide technical information and assists departments in implementing an effective PPE program in the workplace
4. Equipment and Tools:-
- Surveying Equipment
- Mason Trowels
- Ready-mix Concrete Truck
- Concrete Pump
- Concrete Vibrator
- Tower Light (in case of night pouring)
- Electric Generator
5. Compliance to Safety & Protection:-
For every aspect of work of the work, safety awareness shall be strictly followed. In securing permits, relevant IFC drawings shall be attached depending on the location of the area being considered. The following are the minimum safety to be strictly implemented.
- Work Premises – The areas shall be maintained with respect to the tidiness with all materials, tools & equipment’s stacked in appropriate locations to prevent possible disturbance or even worst an accident.
- Safety of Crew – Obviously during casting, the use of proper personnel protective guard or equipment shall be in-force. The use of proper handy tools and work equipment are implemented at all times. All personnel assigned in this area shall have the complete safety protective gears and updated safety information at all times.
- Safety of Crew – Obviously during casting, the use of proper personnel protective guard or equipment shall be in-force. The use of proper handy tools and work equipment are implemented at all times. All personnel assigned in this area shall have the complete safety protective gears and updated safety information at all times.
- Safety Tools & Equipment – Ensure that all mechanical or electrical operated tools and equipment use during these activities are all in working condition.
- Safety in Work Execution.
During concreting work, everyone must be attentive to the sequence of operation. Observe frequently the reactions of the formworks especially when this is hit by the movements of the concrete vibrator during casting. Random check of formworks to be conducted for possible releasing of supports installed. Below are the minimum safety that shall be implemented.
- Tool Box Meeting shall be conducted and potential hazards identified and highlighted to all concern.
- Rubber gloves, goggles and rubber safety boots shall be used while doing concreting.
- Housekeeping shall be maintained at all times.
- Proper stacking of re-bar is to be practiced.
- All metal and wooden scraps to be stacked at designated area.
- Protruding re-bar to be protected.
- Warning signboard must be displayed at the site.
- Steel structural materials in the fabrication yard must be stacked in proper manner.
- Fabrication yard must have at least two fire extinguishers (9Kg).
- At site, adequate instructions should be given to the workers on the methods, arrangements and means required for the construction, storage, transportation, lifting and erection.
- All tools and equipment’s must be inspected and checked before use.
- Proper barricades must be provided and maintain around working area at all times.
- Proper access ways to be maintained unobstructed at all times.
- Hazard identification checklist to be completed by supervisor and potential hazards highlighted during toolbox meeting.
- Check route of concrete trucks for obstructions.
- Reversing of concrete truck shall be done with the aid of a guide man.
- Left over concrete shall be disposed at proper location.
6. Quality Control:-
During execution of works, the assigned quality control engineers that will monitor every step of the work to make sure that requirements of the Project are followed. Request for inspection shall be submitted based on the Quality Project Requirements.
7. Responsibilities:-
7.1 Project Manager:-
Project Manager has the overall authority and responsibility for all aspects of the Project. His responsibilities include as:
- Ensuring adherence with Company Policies.
- Managing site project activities on behalf of The company.
- Establishing project requirements, policies, organization and schedule.
- Monitoring project’s progress and quality, approving final resolution of all items of non- conformance.
- Approving all subcontracts.
- Ensuring implementation of the QA/QC Program.
- Issuing all projects directives.
- Managing project’s costs.
- Initiating and negotiating with client for all change orders and / or work requests and signing change order and / or work requests.
- Preparing, approving and submitting progress reports to the client.
- Having final authority on all site project activities
7.2 Construction Manager:-
The Construction Manager controls and coordinates all work activitiescarried out in the construction site. His responsibilities as:
- Establishment and implementation of work procedures in the MS for the execution of work.
- Review detailed construction schedule including redefinition of priorities where necessary.
- Control and coordination of the work entrusted to Sub-contractors.
- Planning and scheduling of the work force and equipment.
- Review of the materials delivery schedule.
- Preparation of data required for compilation of the Work Progress Report.
- Preparation of the change order proposals.
7.3 Site Engineers:-
- The assigned engineer shall ensure that the current drawings relating to the concrete activity are approved for construction.
- The engineer shall ensure that there are no conflicts with existing services or other discipline issues.
- Co-ordinate all the site activities required for the execution of Work according to the contract
- Liaise with site representatives of Client and Engineer to co-ordinate safety procedures.
- Co-ordinate and explain the work to be carried out to the Supervisors / Site Foreman.
- Ensure the compliance of works with the related approved Quality Control Plan.
7.4 QA/QC Manager:-
-
- Representing the project for all quality matters.
- Developing and maintaining the Project Quality Plan.
- Verifying implementation and adherence with QA/QC.
- Quality Procedures and / or work instruction.
- Preparation of new procedures and / or work instructions.
- Reporting items of non-conformance to the Project Manager.
- Reporting on the corrective action / resolution of non- conformance.
- Verifies program implementation by conducting project specific audits.
- Liaison with client to coordinate and assist in client audits, surveillance, inspections and approvals.
- Establishing, maintaining and overseeing the document control and record keeping function.
- Establishing, maintaining and overseeing the Non-destructive Testing and Wild Engineering functions.
- Quality Monthly Report Preparation.
- Evaluation of Suppliers/ Sub-Contractor’s Quality Systems.
- Coordination and supervision of activities related to the collation of the “Project Record Books”
- Preparation and submission of “Two Week Look Ahead Schedule” requirements.
- Preparation and submission of “Monthly Management Review Reports” on monthly basis.
- Organize Inspection and Test Plan for procurement, construction and commissioning phases.
7.5 QC Inspector:-
- Duties and responsibilities of QA/QC Inspector could be typically enumerated as follows:
- Ensure compliance with the requirements of the contract scope of work, technical specifications and contract quality plan.
- Conduct quality control inspection tasks in accordance with the requirements of the established inspection plans.
- Initiate WIR after verification of activities to be offered for Inspection.
- Signs and dates inspection reports for those inspection steps actually performed. Provides final acceptance sign-off of all prescribed inspection reports attesting to the completeness of the project.
- Calibration and use of the necessary measuring and test.
- Coordinate for the third party agency for the required test.
- Initiate preparation of the job site quality control records.
- Reporting both verbally and in writing any non-conformance discovered.
- Reporting daily a descriptive of each day’s work.
- Conduct weekly QA/QC Toolbox meeting.
- Shall report/coordinate with Client personnel for witnessing all inspections and acceptance of the work items.
7.6 HSE Manager:-
-
- Conduct HSE training for all employees such as toolbox talk, safety awareness training, and safety orientation.
- Investigate injuries, spills, and other incidents and promptly provide corrective actions.
- Determine the cause of any accident (or dangerous occurrence), and recommend means of preventing recurrence of such an incident.
- Plan to Implements all Safety Programs & achieve them.
- Explain Safety Programs in an Easy method to understand all.
- Conduct and document weekly and monthly safety meetings as per client guidelines.
- Identify the unsafe acts and conditions in workplace and correct it promptly.
- Conduct routine safety and environmental inspections and tours.
- Maintain facility emergency plans and conduct regular emergency drills.
- Review organization and employee safety performance periodically and provide feedback.
- Provide Ways to prevent injury to personnel, damage to plant and/or equipment and fires.
- Provide Ways to improve existing Safe work method.
- Follow legal and contractual requirements in safety, health and welfare.
- Identify, evaluate and eliminate the Potential hazards on work site and camps.
- Carry out site surveys to see that only safe work methods are in operation, that health and safety requirements are being observed.
- Ensure welfare and first aid facilities are adequate and properly maintained.
- Recording and analysis of information on injuries, damage and production Assess accident trends and review overall safety performance.
- Conduct safety inspection and safety audit as per the Client guidelines.
- Keep all safety related files and documented properly.
- Circulate safety information to each level of employees.
- Attend jobs progress meetings where safety is an item on the Report on job safety performance.
- Responsible for the implementation of company’s safety program.
7.7 Safety Officer:-
-
- Responsible for the Client’s HSE implementation.
- Liaise with Site Engineers in implementation of site Safety Plan and issue safety directives accordingly.
- Makes sure HSE roles, responsibilities, policies, plans and objectives are communicated to all relevant personnel.
- Ensure that PTW requirements has been secured and must be available at site.
- Liaise with the Project Safety Manager in identifying the HSE training requirements of personnel and assist in arranging internal and external training.
- Investigate accidents and incidents that result in “Lost Time Accidents” (LTA’s).
7.8 Surveyor:-
Surveyor under the direction of the nominated chief surveyor has the responsibility to check the established main reference and check levels at regular intervals.
7.9 Supervisors / Foreman:-
Supervisors have the direct overall responsibility for the supervision of their allocated area including the direct supervision of the fixers and labors involved and the strict implementation of safety rules and procedures.