METHOD STATEMENT OF ICT SYSTEM INSTALLATION, TESTING AND COMMISSIONING
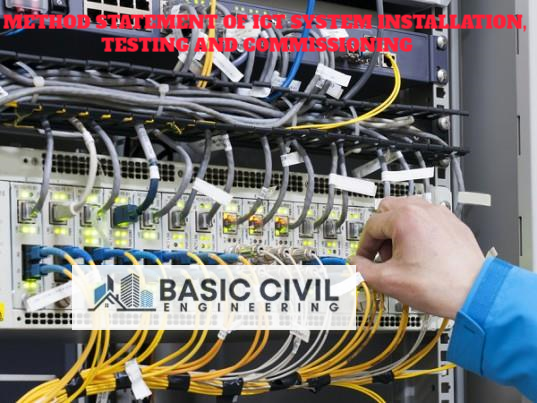
Method Statement Of ICT System Installaltion,Testing And Commissioning
1.PURPOSE:-
This statement has been developed in direction to confirm that the work is in compliance with Quality Control activities during implementation of ICT Components for Design and Construction
2.SCOPE:-
The purpose of this document is to provide minimum requirements for the procedure to be implemented and methods for the storage handling and preservation of materials and installation of ICT Components in accordance with IFC drawings, standards, codes and related specifications and with safety requirements. It is to guide and take precautionary measures and to safeguard traffic within the area of work and possible environmental impact.
This method statement shall be communicated and be understood by all personnel associated with the task before commencing the activity.
3.DEFINITIONS / ABBREVIATIONS:-
- Client/Company: NEOM
- Contractor: TAMIMI GLOBAL COMPANY
- PQP – Project Quality Plan
- ITP – Inspection & Test Plan
- HSE – Health, Safety and Environment
- PPE – Personal Protective Equipment
- ACS- Access Control System
- CCTV- Closed-Circuit Television
4.References:-
- Scope of Works (Installation, Testing and Commissioning of ICT System)
- Project Quality Plan
- Approved ITP
- Project HSE Plan
- Design Drawing / IFC Drawings
- Approved Material:
- BICSI Telecommunications Distribution Methods Manual
- Company Construction Safety Handbook
- OSHA Regulation
- Approved Inspection and Test Plan
- British Standard (BS) 7671 BS 6121, BS 5467 or BS2874
- International Building Code IBC, latest edition in time of tendering
- Saudi Building Code, latest edition in time of tendering
5.LIST OF TOOLS AND EQUIPMENT:-
Telecommunication Hand & Power tools
- Fibre optic Cables
- Horizontal Copper U/UTP Cat 6A Cables
- Data outlets & faceplates
- Cable connecting hardware, patch panels, and patch cords
- Telecommunications equipment racks and cabinets
- Telecommunications service pathways
- Power distribution units (PDU)
- Core
- Access
- CCTV, ACS, AV
- FOC-Fibre Optic Cable
- Optical Network Unit (ONU)
- Telephone
- Electric power tools
- Fish tape
- Multi-tester
- Measuring tape
- Vacuum Cleaner
- Adjustable Wrench
- Insulation tester
- Other Miscellaneous tools and equipment
- Personal Protective Equipment
6.MANPOWER LIST:-
- Site Engineer – IT/ Electrical
- Foreman – IT /Electrical
- Safety Officer
- Work Permit Receiver/Issuer
- Electrician Skilled Workers
- Carpenters
- Labor & Helper (Depends on the actual work )
7.MATERIAL REQUIREMENTS:-
- Indoor Active IT Components shall conform to all applicable requirements, standards, and specifications prior to release to be used as part of the work.
- These shall be inspected for damage/ defects occurred during transportation and handling of the IT equipment.
- IT Components equipment shall be stored away from construction materials, road traffic, falling or flying objects, and areas where there is a risk of physical damage.
- IT Components equipment shall be checked that all supplied items associated components of Indoor Active IT Components are in conformance with the purchase order and specifications data sheets.
- IT Components Equipment shall be traceable from the manufacturer and supplier through delivery, storage, fabrication, erection, installation, repair, modification and use. Indoor IT Components
8.METHOD STATEMENT:-
8.1. DELIVERY, STORAGE AND HANDLING:-
- Deliver products will be in factory Will be Stored in clean, dry, closed space in original containers. Protect products from fumes. Handle very carefully to avoid shocks or damage.
- Software packages Will be supplied in manufacturer’s sealed standard packages
- Inspection shall be performed in two stages, first time upon receiving the equipment, devices and cables on site before storing and second time after installation according to installation phases
- Environmental Limitations: Do not deliver or install cables, devices and equipment until wet work in spaces is complete and dry, and temporary HVAC system is operating and maintaining ambient temperature and humidity conditions during the remainder of the construction period.
- Installation of will not be proceeded unless all necessary hardware (servers/workstations) have been installed, tested and ready for any required software installations.
8.2 GENERAL REQUIREMENT:-
- Approved and valid permit shall be obtained prior to installation of Indoor Active IT Components, as well as during transportation of the equipment to the work site and only appropriate permits shall be used.
- Proper Inspection of Materials as per requirements of approved Material
- All tools and equipment shall be prepared and maintained in good working condition prior to installation of Indoor Active IT Components.
- Workplace shall be evaluated first for any hazards like toxic gas, falling debris, for workmen safety.
- Proper PPE shall be worn. Extra precautions shall be observed. Warning signs shall be visibly posted. Area of lifting shall be barricaded properly. Ensure that only allowed personnel are present on the job Unauthorized personnel shall keep away from the workplace especially during lifting. Certified rigger shall assist the certified equipment operator during loading and unloading of the equipment.
8.3 INSTALLATION OF IT ACTIVE COMPONENTS:-
- Preparation and installation of Indoor Active ICT Components shall be planned, guided and monitored by Site ICT Engineer, ICT Supervisor, and witnessed by Quality Control Inspector and/or Company Project Inspection Division representative/Inspector. All applicable and approved IFC drawings or layouts and Manufacturer’s instructions/drawings shall be available at work site.
- Pulling Cable Precaution: Do not exceed manufacturer’s recommended pulling tensions. Do not install bruised, kinked, scored, deformed, or abraded cable. Do not splice cable between normal termination Remove and discard cable where damaged during installation and replace it with new cable
- All active Equipments like Data switches and servers must be installed by certified
- Verify each Active IT Switch against project data sheets, specifications and
- Indoor Active IT Components shall be mounted on level structural support as per the location drawing and one-line diagram. Mounting shall be in accordance with latest and approved IFC drawings and Vendor documents. Extra care must be provided during lifting operations.
- Precautionary measures shall be observed not to damage the equipment, property and to risk life.
- Identify system components, wiring, cabling, boxes, panels and Comply with requirements for system identification according to project operator requirements.
- System labelling scheme must be submitted to the End user project operator for approval. Operator teams labelling requirements should be considered.
- Indoor Active IT Components shall be installed at a level floor strong enough to support the
- The Active IT Components Installation shall be such that there is easy accessibility for operation and inspection.
- The Active IT Switch position shall be such that the control panel indicator, name plate, can be examined.
- Check that protective grounding is correctly installed to be connected to the main ground
- Properly fix Cover/Panel mounting.
- Contractor will modify the location of data outlets serving the WI-FI network according to the manufacturer design software analysis. every WI-FI access point must have its own data outlets that serves the Wi-Fi access point.
- Wireless Access Points shall be supplied with suitable brackets and mounting plates for installation
- Integration between CCTV & Access control system shall as per requirements.
- The system shall monitor the condition of the inputs. The system shall allow the programming of the way in which these inputs are to be monitored and shall annunciate the condition of such inputs in accordance with such programming.
- The system shall provide a means to control access through nominated doors by checking the access privileges stored in intelligent readers for access control tokens presented at such readers.
- The system shall support unlimited PC based operator workstations simultaneously running on the system.
8.4 FOC and LAN (Structured Cabling System) cable installation:-
- Contractor is fully responsible for supplying, installing, testing, commissioning, put into operation a complete structured cabling system as indicated in the drawings to achieve system requirements indicated in related plans, risers, BOQ, specifications and all related contract documents including all necessary accessories to construct fully functional end-to-end integrated system including-but not limited to-the following:
- Fiber optic Cables (FOC)
- Horizontal Copper U/UTP Cat 6A Cables
- Data outlets & faceplates
- Cable connecting hardware, patch panels, and patch cords
- Telecommunications equipment racks and cabinets
- Telecommunications service pathways
- Power distribution units (PDU)
- Cabling identification
- Grounding
- Interface with external services tie-ins
- Integration with existing system all other related
- Fiber Optic Cable and LAN cable installation should be installed by Certified
8.5 DATA NETWORK ACTIVE EQUIPMENT SYSTEM:-
- Contractor is fully responsible for supplying, installing, testing, commissioning, put into operation a complete data network active equipment system as indicated in the drawings to achieve system requirements indicated in related plans, risers, BOQ, specifications and all related contract documents including all necessary accessories to construct fully functional end-to-end integrated system including-but not limited to-the following:
- Core
- Access
- Optical Network Unit (ONU)
- Telephone
- WIFI access
- Integration with all other related
- Interface with external service provider
8.5 SYSTEM ARCHITECTURE:
The Local Area Network (LAN) consists of a two-layer architectural network:
- Core layer
- Distribution layer
- Access
- A Telecommunications Room (TR) a data center will be provided with new access switches will be installed.
- The access switches will consist of 48/24 PoE+ ports for connectivity to the end
- The LAN shall be resilient and redundant with automatic fail-over to insure that performance and high-availability objectives are met without manual intervention. Recovery mechanisms must be deployed as part of the network implementation and must be tuned to achieve less than 1 second recovery time. All switches shall be interconnected and configured as indicated on network riser diagrams and plans taking into consideration all required redundancy features on both software and hardware levels.
8.6 IPTV SYSTEM:-
- TGC is fully responsible for supplying, installing, testing, commissioning, put into operation a complete IP-Television system as indicated in the drawings to
achieve system requirements indicated in related plans, risers, BOQ, specifications and all related contract documents including all necessary accessories to construct fully functional end-to-end integrated system including-but not limited to-the following:
1.D ish Farm.
2.L ED Screens.
2.I PTV Headend.
2.S et-top box.
8.7 AUDIO-VISUAL SYSTEM:-
- TGC is fully responsible for supplying, installing, testing, commissioning, put into operation a complete audio-visual system as indicated in the drawings to
achieve system requirements indicated in related plans, risers, BOQ, specifications and all related contract documents including all necessary accessories to construct fully functional end-to-end integrated system including-but not limited to-the following:
1.A v Wall-mountable outlet.
2.C ables and connectors.
3.W all-mountable outlet.
4.S mart Screens.
5.S ound bars.
6.C ables and connectors.
7.F eedback Suppressor
8.7 SOUND SYSTEM:-
- TGC is fully responsible for supplying, installing, testing, commissioning, put into operation a complete sound system as indicated in the drawings to achieve
system requirements indicated in related plans, risers, BOQ, specifications and all related contract documents including all necessary accessories to construct fully functional end-to-end integrated system including-but not limited to-the following:
1.A udio Matrix & Controllers.
2.P reamplifiers, power amplifiers.
3.P rogram sources (CD player, tuner).
4.L oudspeakers (Ceiling mounted, wall mounted, Horn speakers, Column speakers, etc.)
5.M onitor module panel.
6.C all Stations.
7.V olume Control.
8.R acks.
9.I ntegration with all other related systems.
8.10 VIDEO SURVEILLANCE SYSTEM (CCTV SYSTEM):-
- TGC is fully responsible for supplying, installing, testing, commissioning, put into operation a complete Video surveillance system (VSS) as indicated in the
drawings to achieve system requirements indicated in related plans, risers, BOQ, specifications and all related contract documents including all necessary accessories to construct fully functional end-to-end integrated system including-but not limited to-the following:
1.I P Cameras.
2.C CTV Workstations
3.V ideo Wall.
4.L ED Screens.
5.I ntegration with all other related systems.
- The main CCTV workstation will be located in the control rooms
- The Workstation Application shall provide the ability to control and program any IP compliant camera.
- Manually control the pan, tilt and lens functions.
- Set the pan and tilt home positions for manual or alarm activation.
- Automatically control the cameras through an alarm Trigger.
- Ability to set multiple pre-set positions.
- Ability to set multiple tours.
- Adjust the zoom lens.
9.Installation Methodology:-
- Install the system as indicated, in accordance with equipment manufacturer’s written instructions (official installation manuals) and complying with applicable local standards of installation. Installation of equipment and devices that pertain to other Works of the Contract shall be closely coordinated with the appropriate trades.
- Pulling Cable: Do not exceed manufacturer’s recommended pulling Do not install bruised, kinked, scored, deformed, or abraded cable. Do not splice cable between normal termination points. Remove and discard cable where damaged during installation and replace it with new cable.
- Identify system components, wiring, cabling, boxes, panels and Comply with requirements for system identification according to project operator requirements.
- System labeling scheme must be submitted to the End user project operator for approval. Operator teams labeling requirements should be considered.
- Install framed operation instructions in visible locations as required.
- As recommended by manufacturers & any specific Operator standards, unless more stringent requirements are indicated. Ground equipment and conductors to eliminate shock hazard and to minimize ground loops, common-mode returns, noise pickup, cross talk, and other impairments. Install Grounding system in complete accordance with system manufacturer’s requirements and BICSI TDMM manual instructions.
- All System Cables should be LSZH produce no toxic gases in case of fire.
- Cables should be listed for the system specific application and installation requirements.
- All wires and cables shall be listed and/or approved by a recognized testing agency & System manufacturer through official letter supported with all necessary calculations, documentations and testing certificates.
- Embedded conduits shall be PVC and all exposed conduits shall be EMT conduit
- All wiring shall be color coded and Junction boxes shall be color coded and include wiring identification numbering.
- Wires and cables shall provide sufficient resistance to the spread of fire and generate no hazardous smoke to human life.
- Wiring System shall include all indoor and outdoor cables necessary for complete system installations.
- Specialist Technician shall be available during connections and splicing.
- To provide suitable distance between ICT cables and Electrical Cables to avoid Noise Interference.
10.Termination and Connection of IT Active Components:-
- The IT enclosure, and IT active component wiring and accessories will be install and will be tested completely as per Manufacturer’s procedure.
- Ensure actual IT Component and cable number is matched with the project specification of the termination Continuity test shall be conducted to ensure right cable to be terminated
- Cable support and other necessary fittings will be properly provided and
- cable trays or Conduits with the indicated types and sizes as per the approved shop drawings, complete with manufacturer’s recommended covers, strips, dropouts, fittings, bolts, conduits adapters, hold-down devices, supports, connectors, bonding jumpers, etc.
- Bending radius shall be considered as per Properly cut the excess length of the cable with Cable Cutter for Termination.
- Properly dress the cable nearly up to the cable entry, and ensure that wires are not cut. Cable waste shall be directly put at the trash bag.
- In between the cable jacket and wire, approved shrinkable sleeve shall be provided and heated by heating gun.
- Proper cable tag shall be provided and properly fixed near the sleeve.
- Cable or wire identification shall be provided as per ferruling.
- Approved cable tagging shall be properly installed. Ensure that it will not unintentionally Proper cable/wire color coding or phasing shall be observed.
- Strip minimal length of insulation of the wire just fitted for the lugs. Insert the bare part of conductor into lugs and compressed by crimping Ensure lugs are properly connected to the conductor.
- Some terminations need to put sleeve between lugs and the core, apply as applicable.
- Prior to cable to be connected to the Active IT Components, continuity and insulation resistance test shall be conducted.
- Connect core at the terminals properly. Shields shall be grounded properly as specified.
- Arrange cable neatly and orderly.
11. Power integration and Grounding:-
- All grounding and bonding requirements mentioned in ANSI-J-STD-607-A/B for all installations using TGBS and TGBMS Should be followed in complete accordance with system manufacturer grounding requirements documents that should be included in the technical material submittal.
- All equipment, Racks, panels and cable shields must be bonded with access toan approved ground connection (clean earth) using TGB “Telecommunication Grounding” according to TIA-607-C.
- Contractor shall coordinate to provide the necessary required power (DC&AC) for all equipment after determining the manufacturer equipment exact part number and hence submit any necessary modifications (if needed) according to selected equipment manufacturer instructions.
12. Testing and Pre-Commissioning:-
- The work to be carried out under this section shall comprise the supply, installation, testing, commissioning and setting to work all items that are necessary for a complete data network active equipment system as per specifications and drawings.
- Contractor will not install any software programs unless all necessary hardware (servers/workstations) have been installed, tested and ready for any required software installations.
- Contractor will provide Testing & commissioning procedures according to system manufacturer requirements and calibration certificate for testing equipment.
Testing & commissioning plan:
- All testing procedures will be submitted for Engineer approval according to manufacturer testing procedures.
- AMT will Submit testing and commissioning procedures including required test equipment for all of the system components as well as the overall system performance.
- All testing equipment and all necessary additional equipment / devices necessary to perform or create a testing environment to simulate the full system operation with its full capacity, are considered in the contractor scope of work without any extra fees.
- Testing devices calibration certificates..
- Testing results shall be submitted in both soft and hard copies for 100% of the system components. Testing shall take place in the engineer presence.
- Testing shall be performed under normal operation conditions for the building i.e in the presence of ambient Electromagnetic interference sources.
- System components factory tests certificates should be submitted with field Testing.
- Software Services for Components.
- Technical Support: Beginning with Substantial Completion, provide software support for 3 years.
- Upgrade Service: Update software to the latest version available at the Project completion. Install and program software upgrades that become available within 3 years from date of Substantial Completion. Upgrading software shall include operating Upgrade shall include new or revised licenses for using of software.
- Provide 30 days’ notice to Owner to allow scheduling and access to system and to allow Owner to upgrade computer equipment if necessary.
- System manufacturer must provide all necessary software development kits (SDKs) necessary to perform all integration requirements.
- Contractor /System integrator must coordinate to handle all necessary SDKs, APIs to achieve all necessary integration requirements.
13. QUALITY CONTROL:-
Receiving Inspection
- Check the availability of “IFC” drawings, vendor manuals and instructions
- Equipment received will be stored according to the installation schedule and manufacturer’s instruction.
- All Material Receiving Inspection to be completed before installation in
position and if any discrepancy found, item will be entered in the punch list and maintain a record.
- Proper protection will be provided against wind, dust, rain corrosion ETC.
- Record inspection report as per SAIC-T- 5501 under SATIP-T-916-01.
Inspection Prior to Installation:
- Pre-fabricated building release note shall be received from civil department prior to installation work.
- Prior to installation of the equipment structural support and openings shall be inspected in order to confirm IFC drawing requirements for dimension, center line coordination, elevation and layout.
- Check that the orientation marks are provided prior to installation.
- Test certificates for the lifting cranes, tools & tackles, rigger and approved lifting plan shall be made available & accepted by HSE person.
- All the tools and tackles used for installation works shall be of good
- Lifting space availability shall be verified.
- If needed Temporary platform or scaffolding (when required) shall be fixed prior to lifting the equipment.
- Safety personnel shall be informed about all the heavy lifts well in advance.
- The erection area shall be cordoned off and proper signboards shall be provided.
- Record inspection report as per various SAIC-T-5927 under SATIP-T-916-01.
Assembly:
Contractor shall ensure site assistance of the equipment Vendor support specialized person present & supervise if warranted during assembly of the Indoor Active IT Components.
- RFI shall be raised 24 hours before the actual schedule for Inspection as per the approved/applicable SATIP.
- Extreme care shall be taken against any entry of foreign contaminants into the Active IT Components during assembly or internal inspection.
- No blank plate or access disk shall be opened or removed from the equipment assembly if there is slightest possibility of disturbed environmental changes (sand storm, dust cloud, rain or heavy humidity).
- Any open earthworks or grading operation within the local vicinity of the Active IT Components erection / installation shall be suspended until the equipment installation are completed.
- The number of tools used inside the Active IT Components shall be counted before and after work, in order to ensure that none left inside.
- Examine the inside for dirt deposit and clean them as per Vendor Manual.
- All installation shall be carried out as per Vendor Manual.
Pre-Installation Inspection
- Check nameplate ratings are as per Material Technical Approval and project LV Indoor Active IT Components specifications.
- Check the Package equipment are located in the proper location as per IFC
- Check any possible system IT revisions are compatible and functional with both system and Active IT Switch as per project IFC drawings.
- Ensue unattached accessory equipment to be installed after installation is available with all mounting hardware necessary to install as per Manufacturer’s drawings.
- Check all attached equipment for installation on the Active IT Components is aligned and installed properly as per Manufacturer’s drawings.
- Ensure that the nameplate data matches the information illustrated in the Single Line Diagram of project IFC drawings.
- Ensure that all equipment, accessories, and components listed on the bill of materials are present.
- Ensure that there are no signs of external damage.
- Ensure that paint finish has not been damaged; otherwise, it shall be repaired as perManufacturer.
- Ensure that fittings and other attachments are tight and undamaged.
- Check for damage to shipping crates, packages, or other materials shipped separately from the Active IT Components’ enclosures.
- Check that the installation complies as per slint standards.
TESTING
- The following IT test shall be completed with Company Pre-commissioning form before energizing/power up the Indoor Active IT Components:
- LAN Test Cable Continuity and Insulation Testing for installed cable.
- The quality of the works shall be carried out in line with the Project Quality standards.
- Relevant inspections shall be made in stages as per the approved ITP’s.
- Contractor QA/AC inspectors shall closely monitor and assure all general materials shall comply with project specifications and as per Company – QA/QC requirements.
- Inspections shall be conducted all records shall be maintained as required by project QA/QC program in accordance with approved project Quality plan & ITP’s.
- 3rd Party Activity if any must be aligned with every activity necessary for testing as evidence of compliance in Project Requirements.
14.RESPONSIBILITY:-
Project Manager
- The Project Manager shall be responsible for the over-all direction, coordination and control of all the activities.
- Approving all reports regarding the project.
- Contractor interactions and responses
- Reviewing and coordinating Construction Schedules, making schedules forward planning and forecasts.
- Establishing, maintaining and assuring the minimum standards for safety and housekeeping, which are under the jurisdiction of Subcontractor on Site.
- Enforcing adherence to the approved Technical Documents. Approving and accepting the programs, planning, construction schedules, Manpower and equipment usage, in order to accomplish the work.
- To inform Home Office on the current status of such items as progress, Cost, Quality Control and any site problems, through reports.
- To, liaise, as necessary with the Contractor Statutory Authorities, , in order to ensure that the statutory regulations regarding the conditions of work and welfare, for Subcontractor personnel are being complied with.
- To maintain a clean, safe and efficient site.
- To approve Site expenditures within the Project Manager’s designated area of responsibility and in accordance with the financial limits set by Subcontractor and/or the Contractor.
- To liaise, as necessary and inform the Contractor on the current status of construction works, by report and / or Letter in accordance with the Contract to ensure good quality workmanship.
- Coordinating and ensuring that all Subcontractor personnel on Site comprehend and perform their duties proficiently and completely appreciate their responsibilities and involvement in being part of a dedicated Site team.
Construction Manager:-
- Overall construction in charge of construction activities in the project site.
- To supervise and direct the Superintendents and their organizations.
- To assist the Project Manager in job planning and scheduling, and cost control.
- Co-ordination and control activities for Superintendents/Craft Supervisors /Foreman to ensure the most efficient construction operations.
- To control the assignment of major construction equipment required by various crafts with the assistance of Construction Equipment Supervisors.
- To assist with the Project Manager in Establishing, Maintaining and assuring the Minimum standards for safety and Housekeeping.
QA/QC Manager:-
- Responsible for the overall Quality Control of all the construction activities at
- Responsible for all Inspections at Site, inclusive of witnessing, sentencing, recording and reporting the results, and resolving any problems arising.
- Ensure that all inspections are executed efficiently and expeditiously in order to comply with the Master Construction Schedule.
- Responsible for co-ordinating, advising and instructing the Subcontractor Managerial Staff on all matters relative to Quality Control at SITE.
- Establish, implement and maintain all the Site Quality Control technical documents, and any computer integrated control system assure all Technical Documents relative to Site Quality Control are current status.
- Verify detailed records and reports for all Inspections conducted at the Site, and maintain the Quality Control Documentation.
- Establish and conduct regular Quality Control meetings with the Correlate, prepare and issue the Weekly Field Inspection Notice to the Contractor.
- Evaluate specific Inspections and sentence the results where applicable to the
- Prepare and issue Non-conformance Reports, resolve by developing and implementing corrective measures.
- Co-ordinate and conduct Inspections with any applicable local authority.
- Maintain all relative Site inspection records, for handover to Contractor upon attaining Completion.
- Arrange for Inspections on materials and/or equipment when requested by the Material Controller.
- Co-ordinating internally, to ensure correct communications exist and are maintained, between different Subcontractor disciplines.
Safety Manager:-
- Responsible for the overall safety of personnel materials and equipment during the construction and pre-commissioning of a Project.
- The Safety Manager must be fluent conversant in the relative Safety Regulations the Contractor and the Laws and Regulations of the Country in which the Project is to be constructed, ensuring all the operations at the Site are conducted to the minimum safety standards, and that they are maintained throughout construction.
- Co-ordinate and preside over regular site safety meetings, to attain and maintain effective communications, between Subcontractor, Contractor and Company personnel.
- Establish policies and procedures for Subcontractor which comply with the standard Subcontractor policies, the applicable rules and regulations of the Contractor / Company and those of the Country in which the Project is to be constructed and monitor to ensure compliance.
- Establish the safety rules and regulations for site equipment and its usage and mentor to ensure compliance.
- Issue Safety Reports.
- Recognise, recommend and enforce corrections to any unsafe practices, which may occur on site during the construction.
- Prepare and process Accident and Incident Reports.
- Organise special safety training sessions for Subcontractor site personel.
- Prepare and submit the overall activity reports of the Safety Department to the resident construction management.
Environmental Manager:-
- Implementing environmental policies and practices.
- Devising the best tools and systems to monitor performance and to implement strategies.
- Ensuring compliance with environmental legislation.
- Assessing, analysing and collating environmental performance data and reporting information to internal staff, clients and regulatory bodies.
- Confirming that materials, ingredients and so on are ethically or environmentally sourced Managing environmental strategy budgets.
- Liaising with internal staff including senior managers and directors.
- Acting as a champion or cheerleader for environmental issues within your organisation Providing environmental training to staff at all levels.
- Writing plans and reports.
- Keeping up to date with relevant changes in environmental legislation and initiatives including international legislation where applicable.
- Producing educational or information resources for internal staff, clients or the general public.
Telecom Engineer / Supervisor:-
- The Site Supervisor shall be directly involved in the planning and execution of the activities involve. He shall likewise ensure the implementation of quality plans. He shall prepare prior to the start of any work, Safety Action Plan that must be implemented and observed during the work.
- Supervise the site work under the instruction of the Electrical superintendent and in close co- operation with other staffs. Responsible for the following duties.
- Organizing and supervising quality control and cost planning, and keeping close liaison with the Site Superintendent Interpreting and engineering stand point design drawings and specifications for the field force.
- Supervising compilation of job construction schedules and monthly progress reports and reports. Originating correspondence regarding engineering or construction and design matters for the signature of the Project Manager.
- Administering and maintaining the calculated completion percentages
- Reviewing the estimate of physical completion percentages.
- Correlating calculated and estimated completion percentages records for presentation to the Planning Manager.
- Reviewing material status reports, analyzing notes of items being delayed, preparing comments and submitting them to the concerned Superintendent.
- Supervising compilation of field cost reports, checking and tracking field costs, recommending remedial measurement to concerning adverse trends.
- Receipt reproduction and timely distribution to the field of drawings, specifications and other engineering documents. Providing input for the “as-built’ drawings.
- Anticipation and assessment of manpower Co-ordination with the Superintendent on the deployment of construction equipment and construction tools.